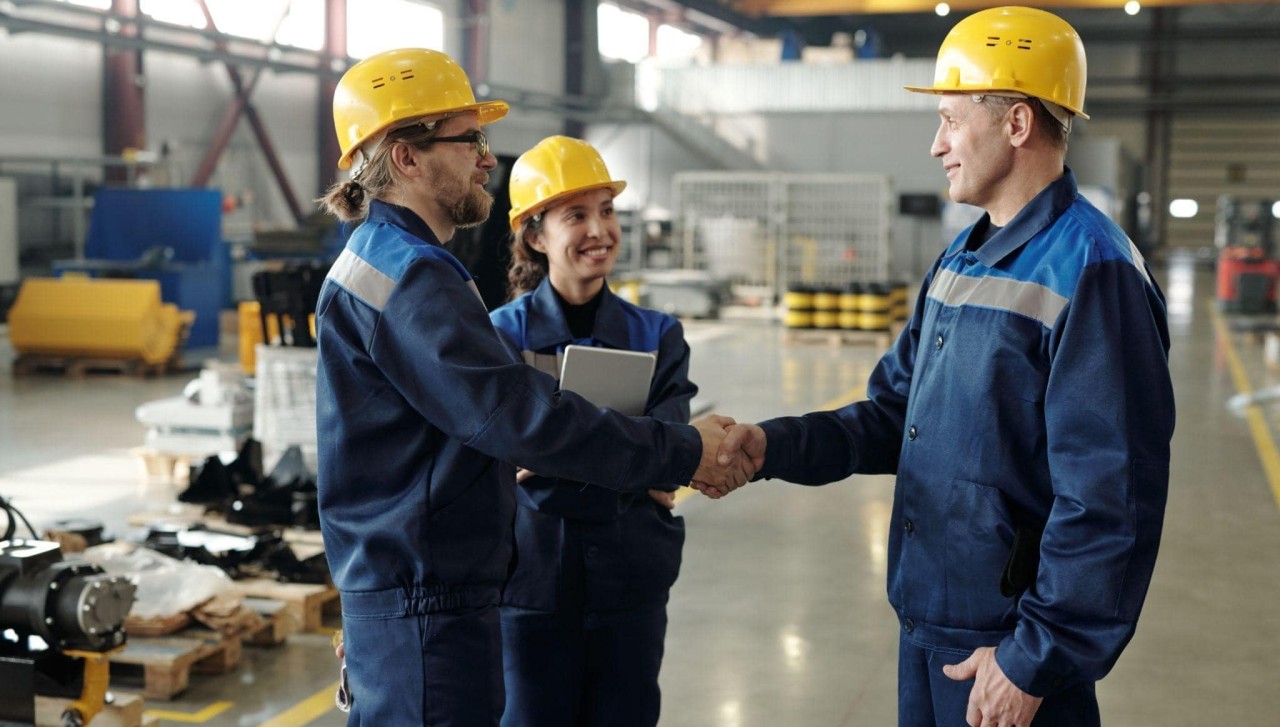
Внедрение искусственного интеллекта (ИИ) в производственные процессы – это не просто модный тренд, а насущная необходимость для повышения эффективности, сокращения затрат и обеспечения конкурентных преимуществ. Современные предприятия, особенно в сегментах малого и среднего бизнеса, сталкиваются с рядом сложностей при интеграции ИИ в процессы фрезеровки и токарной обработки. Игнорирование этих возможностей может привести к технологическому отставанию, увеличению операционных расходов и снижению качества конечной продукции.
Преимущества и вызовы внедрения ИИ в металлообработке
Внедрение ИИ в производство открывает новые горизонты для оптимизации и автоматизации процессов. Однако, наряду с многочисленными преимуществами, предприятия сталкиваются с рядом вызовов:
- Высокая стоимость внедрения и обслуживания систем ИИ. Инвестиции в современное оборудование и программное обеспечение требуют значительных финансовых ресурсов, особенно на начальном этапе.
- Нехватка квалифицированных специалистов. Для эффективной эксплуатации ИИ необходимы специалисты, способные анализировать данные и настраивать алгоритмы машинного обучения.
- Сложности интеграции с существующим оборудованием. Традиционные производственные линии зачастую требуют модернизации для обеспечения корректного взаимодействия с новыми цифровыми технологиями.
- Вопросы надежности и безопасности. Внедрение ИИ требует тщательного анализа рисков, связанных с кибербезопасностью и отказами оборудования.
- Ограниченное понимание возможностей ИИ. Недостаток информации и опыта может привести к завышенным ожиданиям или неправильной интерпретации результатов работы системы.
Что такое искусственный интеллект в фрезеровке и токарной обработке?
В контексте металлообработки, искусственный интеллект представляет собой комплекс компьютерных систем и алгоритмов, способных обучаться, адаптироваться и принимать решения на основе анализа больших объемов данных, получаемых с оборудования и производственных линий. Это позволяет не только автоматизировать рутинные задачи, но и оптимизировать параметры обработки, прогнозировать потенциальные поломки и повышать качество конечной продукции. При этом ИИ не заменяет оператора, а становится его мощным помощником, освобождая время для решения более сложных и творческих задач.
Основные функции и возможности ИИ в металлообработке
Технологии ИИ открывают широкие возможности для оптимизации процессов фрезеровки и токарной обработки:
Автоматическая генерация программ ЧПУ. Современные алгоритмы способны анализировать чертежи деталей и автоматически генерировать оптимальные программы для станков с ЧПУ, учитывая материал заготовки, требуемую точность и другие технологические параметры. Это позволяет значительно сократить время подготовки производства и снизить вероятность ошибок, вызванных человеческим фактором. Например, при выполнении токарно-фрезерных работ на ЧПУ ИИ подбирает оптимальные режимы резания.
Оптимизация режимов резания. ИИ использует данные, поступающие с датчиков (вибрация, температура, ток), для автоматической регулировки параметров резания в режиме реального времени. Такой подход позволяет максимизировать производительность и минимизировать износ инструмента. Например, при фрезеровке стали система автоматически корректирует скорость подачи и глубину резания для достижения наилучшего результата.
Прогнозирование поломок оборудования. Анализируя данные о состоянии оборудования, ИИ способен выявлять ранние признаки износа или приближающихся поломок, что позволяет проводить профилактическое обслуживание и предотвращать дорогостоящие простои. Это особенно актуально при серийном изготовлении деталей, где остановка производства может негативно сказаться на сроках поставок.
Контроль качества в реальном времени. Системы ИИ, оснащенные камерами и датчиками, осуществляют мониторинг параметров обрабатываемых деталей, выявляя дефекты и отклонения от стандартов. Такой контроль позволяет оперативно корректировать технологический процесс и предотвращать выпуск бракованной продукции. Например, при фрезеровке нержавеющей стали ИИ отслеживает шероховатость поверхности и автоматически корректирует режимы резания.
Адаптивное управление производством. Системы ИИ анализируют данные о загруженности оборудования, запасах материалов и текущих заказах, что позволяет автоматически корректировать производственный план. Такой подход особенно эффективен при аутсорсинге производства, где гибкость и оперативное реагирование на изменения спроса играют ключевую роль.
Классификация ИИ-систем для металлообработки
Существует несколько категорий ИИ-систем, каждая из которых предназначена для решения конкретных задач в области фрезеровки и токарной обработки:
- Системы автоматического программирования ЧПУ. Используют алгоритмы машинного обучения для генерации оптимальных программ на основе чертежей деталей и технологических параметров. Пример: системы для 5-координатных станков.
- Системы оптимизации режимов резания. Применяют датчики и алгоритмы для динамической регулировки параметров резания с учетом материала заготовки и состояния инструмента. Пример: системы, оптимизирующие режимы резания при фрезеровке титана.
- Системы предиктивного обслуживания. Анализируют данные о состоянии оборудования для прогнозирования износа и поломок, позволяя проводить своевременное профилактическое обслуживание. Пример: системы, предсказывающие износ инструмента при токарной обработке металла.
- Системы контроля качества. Используют компьютерное зрение и алгоритмы анализа изображений для мониторинга параметров обработки в реальном времени. Пример: системы, контролирующие качество поверхности при фрезеровке алюминия на заказ с использованием ЧПУ.
- Системы управления производством. Автоматически корректируют производственные планы на основе анализа данных о загрузке оборудования, запасах и заказах.
Пошаговая инструкция по внедрению ИИ в производственные процессы
Внедрение ИИ требует комплексного подхода и тщательного планирования. Ниже приведена подробная инструкция, которая поможет успешно интегрировать ИИ в процессы фрезеровки и токарной обработки:
- Определите цели и задачи. Четко сформулируйте ожидаемые результаты: снижение брака, увеличение производительности или сокращение затрат на обслуживание оборудования.
- Соберите данные. Проведите аудит текущих процессов, соберите информацию о работе оборудования, технологических параметрах и качестве продукции. Эти данные станут основой для обучения ИИ-моделей.
- Выберите подходящую систему ИИ. Исследуйте рынок, оцените предложения различных поставщиков и выберите систему, соответствующую вашим требованиям и бюджету.
- Интегрируйте ИИ с оборудованием. Проведите модернизацию производственных линий при необходимости и настройте взаимодействие новой системы с существующим оборудованием.
- Обучите модели ИИ. Используйте собранные данные для обучения алгоритмов. Чем больше и качественнее данные, тем точнее будут прогнозы и рекомендации.
- Проведите тестирование. Испытайте систему в реальных условиях производства, внесите коррективы и убедитесь в достижении поставленных целей.
- Обучите персонал. Проведите тренинги для операторов и инженеров, чтобы они могли эффективно взаимодействовать с новой системой и использовать её возможности.
- Обеспечьте регулярную поддержку и обновление. Постоянно анализируйте работу системы, обновляйте модели по мере накопления новых данных и следите за техническим состоянием оборудования.
Совет: Начните с пилотного проекта. Запустите ИИ в одном или двух ключевых процессах и постепенно расширяйте область применения, оценивая результаты и нарабатывая опыт.
Распространенные ошибки при внедрении ИИ
Для успешной интеграции ИИ в процессы металлообработки важно избегать следующих ошибок:
- Недостаточная подготовка данных. Качество обучающих данных напрямую влияет на эффективность работы системы. Неполные или нерелевантные данные могут привести к ошибочным прогнозам.
- Неправильный выбор системы ИИ. Разные решения ориентированы на различные задачи, поэтому важно подобрать систему, оптимально соответствующую вашим технологическим требованиям.
- Ошибки при интеграции. Неправильная настройка связи между ИИ и оборудованием может привести к сбоям и неверным данным.
- Недостаточное обучение персонала. Без надлежащего обучения операторы не смогут в полной мере использовать потенциал новой системы.
- Отсутствие поддержки и обновлений. Технологии развиваются стремительно, и регулярное обновление ИИ-систем является залогом их актуальности и надежности.
- Переоценка возможностей ИИ. Хотя ИИ является мощным инструментом, он не решит все проблемы. Реалистичные ожидания и понимание его ограничений помогут избежать разочарований.
Характеристики ИИ-систем для фрезеровки и токарной обработки
Характеристика | Свойство | Область применения | Особенности |
---|---|---|---|
Автоматическая генерация программ ЧПУ | Генерация оптимальных программ на основе чертежей | Фрезеровка, токарная обработка | Сокращает время подготовки, снижает риск ошибок |
Оптимизация режимов резания | Динамическая корректировка параметров резания | Фрезеровка, токарная обработка | Повышает производительность, снижает износ инструмента |
Предиктивное обслуживание | Прогнозирование поломок оборудования | Фрезеровка, токарная обработка | Обеспечивает своевременное обслуживание, предотвращает простои |
Контроль качества | Мониторинг параметров в реальном времени | Фрезеровка, токарная обработка | Обнаруживает дефекты и корректирует технологический процесс |
Адаптивное управление производством | Корректировка плана на основе анализа данных | Производство деталей | Максимизирует эффективность, оптимизирует издержки |
Перспективы развития ИИ в металлообработке
С развитием технологий и увеличением вычислительных мощностей, применение ИИ в металлообработке продолжит совершенствоваться. В ближайшие годы можно ожидать:
- Расширение функционала ИИ-систем. Новые алгоритмы и модели позволят достигать еще более высокой точности при автоматизации сложных технологических процессов.
- Увеличение скорости обработки данных. Повышение вычислительных мощностей позволит системам ИИ принимать решения практически мгновенно, что критически важно в условиях высокой производственной нагрузки.
- Интеграция с IoT и облачными технологиями. Объединение ИИ с Интернетом вещей позволит создать полностью автоматизированные и взаимосвязанные производственные линии, способные оперативно реагировать на изменения в режиме реального времени.
- Усиление роли ИИ в контроле качества. Развитие компьютерного зрения и сенсорных технологий позволит проводить еще более детальный анализ изделий, минимизируя человеческий фактор.
Внедрение ИИ с Симиди
Переход к инновационным технологиям – сложный, но крайне перспективный процесс. Для достижения максимальной эффективности и получения реальных конкурентных преимуществ рекомендуется сотрудничество с опытным партнером. Симиди – производственно-инжиниринговая компания, занимающаяся поставкой оборудования, узлов и деталей для предприятий. Мы постоянно следим за новыми трендами в сфере автоматизации, включая Будущее автоматизации: как искусственный интеллект меняет металлообработку.
Свяжитесь с нашими представителями, чтобы обсудить ваши потребности и узнать, как мы можем помочь оптимизировать производственные процессы с помощью ИИ. Дополнительно, вы можете ознакомиться с деталями токарной обработки оргстекла или другими нашими услугами.
Таким образом, интеграция ИИ в процессы фрезеровки и токарной обработки не только повышает качество продукции, но и способствует значительному снижению производственных затрат. Постепенное внедрение, качественная подготовка данных и профессиональная поддержка являются ключевыми факторами успешного перехода к умным производственным технологиям.