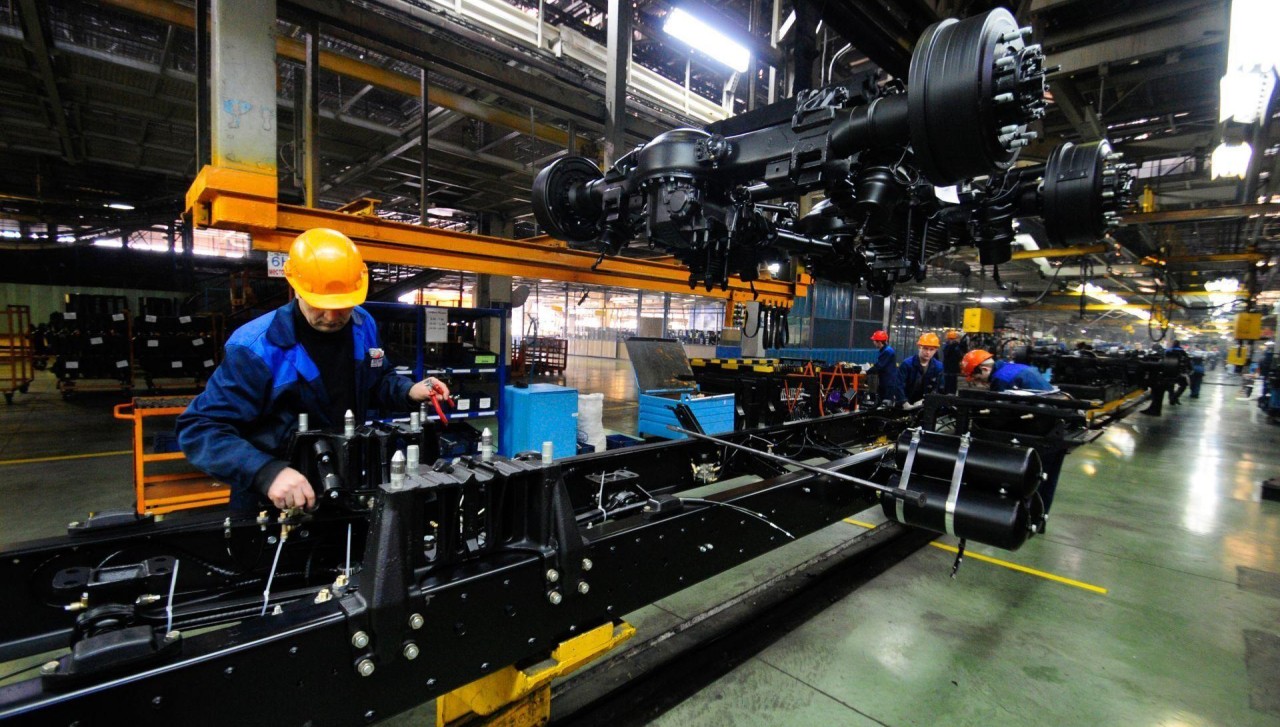
Представьте: от надежности одной маленькой детали зависит работа огромного механизма, безопасность людей и успех целого предприятия. Это не просто слова, а реальность современной машиностроительной отрасли. Ошибка в выборе подхода к производству компонентов может обернуться не только значительными финансовыми потерями, но и серьезными репутационными рисками, срывом сроков и даже угрозой безопасности эксплуатации оборудования.
Машиностроение – это сложная и многогранная отрасль, где качество каждой изготовленной детали напрямую влияет на надежность и эффективность конечного продукта. Современные производственные линии требуют от специалистов не только глубоких технических знаний, но и постоянного внедрения инновационных решений. Игнорирование современных технологий, неправильный выбор материалов или недостаточный контроль качества могут привести к ряду серьезных проблем, таким как:
- Снижение срока службы оборудования;
- Повышенные затраты на ремонт и обслуживание;
- Срывы производственных планов;
- Ухудшение конкурентоспособности продукции;
- Угрозы безопасности эксплуатации.
Как же выбрать правильный путь? Какие сложности приходится преодолевать предприятиям, стремящимся к совершенству в производстве компонентов для машиностроения? Рассмотрим основные вопросы:
- Выбор оптимальной технологии производства: фрезерная или токарная обработка?
- Поиск квалифицированных специалистов и организация непрерывного обучения персонала;
- Внедрение и освоение передовых технологий, таких как системы автоматизированного управления и мониторинга;
- Обеспечение соответствия продукции мировым стандартам качества;
- Оптимизация производственных затрат;
- Сокращение сроков изготовления деталей при сохранении высокого качества.
Что такое токарная обработка металла?
Токарная обработка металла – это метод механической обработки, при котором заготовка вращается, а режущий инструмент (токарный резец) перемещается относительно нее, снимая слой материала и формируя деталь требуемой формы и размеров. Этот способ широко используется для изготовления деталей вращения: валов, осей, втулок, колец, фланцев и множества других элементов.
Современные токарные станки делятся на универсальные и специализированные. Станки с числовым программным управлением (ЧПУ) обеспечивают высокую точность и производительность, что позволяет изготавливать детали сложной геометрии с минимальными допусками. В дополнение к традиционным методам обработки, современные технологии интегрируют системы мониторинга состояния инструмента и автоматизированные системы контроля качества, что снижает риск брака и повышает эффективность производства.
Ключевые функции и возможности токарной обработки
Токарная обработка – универсальный метод, позволяющий выполнять широкий спектр операций для получения деталей с заданными характеристиками. Рассмотрим основные виды обработки:
Наружная токарная обработка: Этот процесс включает обточку цилиндрических и конических поверхностей, подрезку торцов, отрезку заготовок, а также нарезание резьбы. Примером может служить обточка вала двигателя для обеспечения его точного соответствия заданным размерам.
Внутренняя токарная обработка: Операции по расточке отверстий, зенкерованию, развертыванию и нарезанию внутренней резьбы. Например, расточка отверстия в корпусе редуктора для установки подшипника.
Фасонная токарная обработка: Изготовление деталей сложной формы, таких как кривошипы, эксцентрики, кулачки. Пример – создание кулачка для механизма управления клапанами двигателя.
Токарно-фрезерная обработка: Комбинированный метод, позволяющий выполнять как токарные, так и фрезерные операции на одном станке. Это дает возможность изготавливать детали с комплексной геометрией, сочетая преимущества обоих методов. Например, деталь, требующая обработки вращением и фрезерования пазов или плоскостей.
Разновидности токарной обработки и материалов
Процесс токарной обработки классифицируется по различным признакам – типу используемого оборудования, обрабатываемым материалам и требуемой точности. Ниже представлены основные классификации:
По типу оборудования:
- Универсальные токарные станки: Подходят для выполнения широкого спектра операций и часто используются в малосерийном производстве.
- Токарные станки с ЧПУ: Обеспечивают высокую точность, стабильность и производительность, что особенно важно при серийном производстве.
- Токарно-карусельные станки: Предназначены для обработки крупногабаритных деталей, где требуется равномерное распределение нагрузок.
- Многошпиндельные токарные автоматы: Идеальны для массового производства простых деталей, обеспечивая высокую скорость и повторяемость операций.
По виду обрабатываемого материала:
- Токарная обработка металла: Самый распространенный вид, применяемый для обработки стали, чугуна, цветных металлов и сплавов. Например, токарная обработка нержавейки требует особого подхода из-за высокой прочности материала и склонности к налипанию на режущий инструмент.
- Токарная обработка пластика: Используется для создания деталей из полиамида, полиэтилена, полипропилена и других видов пластика, где важны точность и эстетика.
- Токарная обработка дерева: Применяется для изготовления декоративных элементов, мебели и других изделий, где ценятся уникальность и натуральная текстура материала.
По требуемой точности:
- Грубая токарная обработка: Предназначена для предварительной обработки заготовок и подготовки их к дальнейшим высокоточным операциям.
- Чистовая токарная обработка: Обеспечивает получение деталей с высокой точностью размеров и качественной шероховатостью поверхности.
- Прецизионная токарная обработка: Используется для изготовления деталей, требующих исключительно высоких допусков и минимальных отклонений.
Пошаговая инструкция: токарная обработка детали
Процесс токарной обработки проходит несколько последовательных этапов, каждый из которых играет ключевую роль в достижении требуемого качества изделия:
- Подготовка чертежа и технической документации: Определяются размеры, форма, материал и требуемая точность детали. На этом этапе важно уделить внимание каждой мелочи, чтобы избежать ошибок в дальнейшем.
- Выбор материала заготовки: Материал должен соответствовать требованиям технической документации и условиям эксплуатации готовой детали.
- Подготовка оборудования: Выбирается оптимальный токарный станок, устанавливаются соответствующие режущие инструменты и настраиваются технологические параметры обработки.
- Установка и закрепление заготовки: Заготовка надежно фиксируется в патроне или специальном приспособлении, что гарантирует стабильность во время обработки.
- Основной этап обработки: Выполняются все необходимые токарные операции в соответствии с технологической картой, с контролем основных параметров процесса.
- Контроль качества: Проводится измерение размеров, проверка шероховатости поверхности и соответствия детали установленным требованиям. Часто используется автоматизированный контроль для повышения точности.
Пример: Изготовление вала редуктора:
- Выбор материала: сталь 45;
- Операции: обточка, подрезка торцов, нарезание резьбы;
- Инструмент: токарные резцы из быстрорежущей стали или твердого сплава;
- Контроль: измерение диаметра, длины, шага резьбы.
Совет: Для повышения точности обработки рекомендуется использовать охлаждающие жидкости. Они не только уменьшают трение, но и эффективно отводят тепло из зоны резания, что позволяет продлить срок службы инструмента и улучшить качество поверхности детали.
Расширенные аспекты современной токарной обработки
С развитием технологий традиционные методы обработки претерпевают существенные изменения. Ниже представлены некоторые из ключевых направлений инноваций в токарной обработке:
- Интеграция с цифровыми технологиями: Применение CAD/CAM-систем позволяет моделировать процессы обработки, прогнозировать потенциальные отклонения и оптимизировать траекторию резания.
- Автоматизация и роботизация: Внедрение роботизированных систем для загрузки и выгрузки заготовок снижает влияние человеческого фактора и повышает производительность.
- Системы мониторинга состояния инструмента: Современные датчики и системы обратной связи позволяют в реальном времени контролировать состояние режущего инструмента и своевременно проводить его замену или ремонт.
- Экологическая безопасность и энергоэффективность: Новые технологии обработки направлены на снижение энергопотребления и уменьшение количества отходов, что соответствует современным требованиям устойчивого развития.
Распространенные ошибки и как их избежать
Даже при наличии современного оборудования и квалифицированных специалистов могут возникать ошибки, приводящие к браку и увеличению затрат. Знание основных ошибок и способов их предотвращения поможет оптимизировать процесс производства:
Ошибка 1: Неправильный выбор режима резания.
Последствия: Преждевременный износ инструмента, низкое качество поверхности, вибрации и поломки оборудования.
Рекомендации: Тщательно подбирайте параметры резания (скорость, подачу, глубину резания) с учетом материала заготовки, типа инструмента и требуемой точности. Используйте технические справочники и рекомендации производителей режущих инструментов.
Ошибка 2: Неправильный выбор режущего инструмента.
Последствия: Плохое качество обработки, быстрый износ инструмента и невозможность работы с твердыми материалами.
Рекомендации: Выбирайте инструмент, оптимально соответствующий материалу заготовки и характеру операции. Для обработки твердых материалов применяйте инструменты из твердых сплавов или керамики. Например, для токарной обработки молибдена требуются специальные резцы.
Ошибка 3: Недостаточное закрепление заготовки.
Последствия: Вибрации, смещение заготовки и неточность размеров готовой детали.
Рекомендации: Обеспечьте надежное крепление заготовки с использованием специальных патронов и приспособлений, особенно при обработке деталей сложной формы.
Ошибка 4: Отсутствие или недостаточное использование охлаждающей жидкости.
Последствия: Перегрев инструмента, налипание материала на режущую кромку и ухудшение качества поверхности.
Рекомендации: Применяйте охлаждающие жидкости, подобранные с учетом типа обрабатываемого материала и особенностей операции. Это позволит не только снизить трение, но и обеспечить стабильность технологического процесса.
Сравнительная таблица характеристик материалов для токарной обработки
Материал | Свойства | Область применения | Особенности |
---|---|---|---|
Сталь 45 | Высокая прочность, хорошая обрабатываемость | Валы, оси, шестерни | Поддается термообработке |
Алюминий Д16Т | Легкий, прочный, коррозионностойкий | Корпуса, детали авиационной техники | Требует применения специальных смазочно-охлаждающих жидкостей |
Титан ВТ1-0 | Высокая прочность, коррозионная стойкость, малый вес | Детали ракетных двигателей, медицинские имплантаты | Сложная обработка, требует применения твердосплавного инструмента |
Фторопласт Ф4 | Низкий коэффициент трения, химическая стойкость | Уплотнения, подшипники скольжения | Легко обрабатывается, но имеет низкую прочность |
Капролон | Износостойкость, хорошие антифрикционные свойства | Втулки, шестерни, подшипники | Хорошо поддается обработке, но требует контроля температуры для предотвращения деформации |
Выбор надежного партнера в производстве компонентов для машиностроения
Выбор правильного подхода к производству компонентов – задача, требующая глубоких знаний, опыта и современного оборудования. Симиди – это производственно-инжиниринговая компания, специализирующаяся на изготовлении и поставке оборудования, узлов и деталей для предприятий различных отраслей промышленности. Компания предлагает полный цикл услуг: от проектирования до серийного производства, гарантируя высокое качество и соответствие продукции самым строгим стандартам.
Не уверены, какой метод обработки подойдет для вашего проекта? Хотите узнать больше о возможностях аутсорсинга производства? Свяжитесь с представителями Симиди для получения консультации и индивидуального предложения. Их эксперты помогут выбрать оптимальное решение, которое обеспечит высокое качество, надежность и эффективность работы ваших машин и механизмов.
Современный рынок машиностроения требует постоянного развития и адаптации к новым технологиям. Инвестиции в автоматизацию, цифровизацию производства и повышение квалификации персонала – залог успеха в условиях жесткой конкуренции. Выбирайте надежного партнера и инновационные подходы для достижения лидерства в своей отрасли!