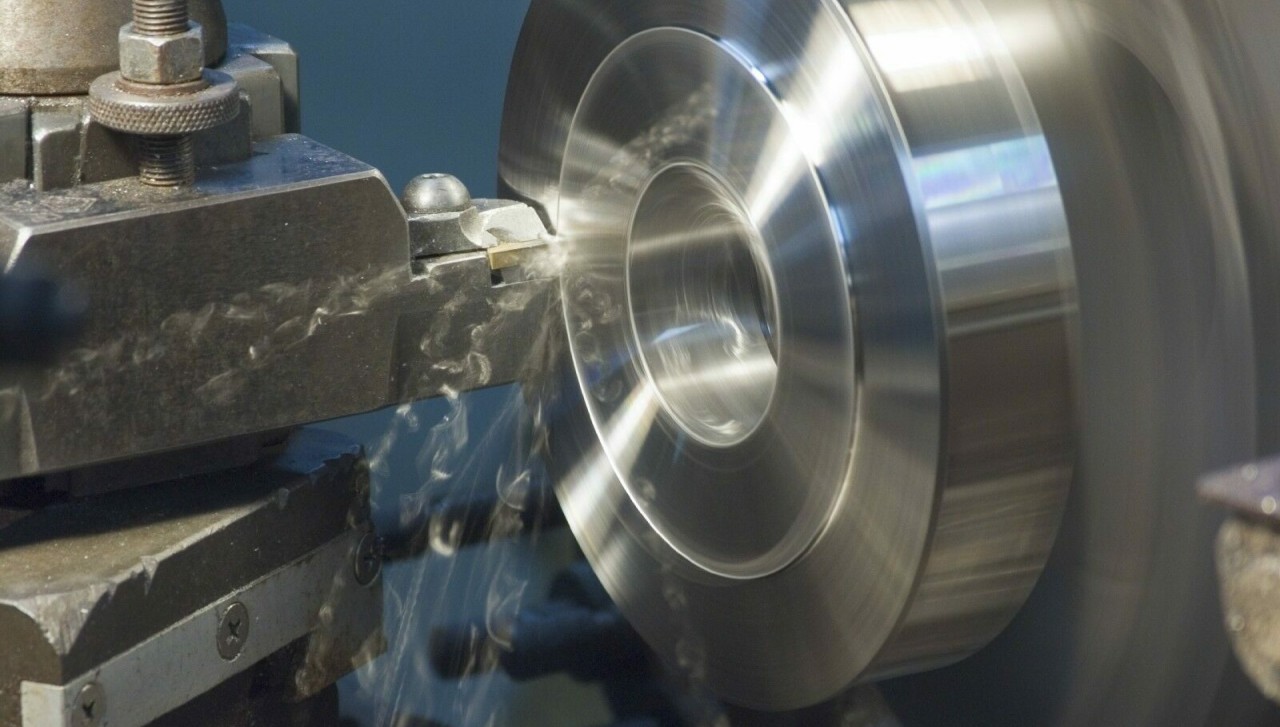
От небоскребов и автомобилей до медицинского оборудования и бытовой техники – сталь является основой современной инфраструктуры. Технологии её обработки, в частности токарная обработка, играют ключевую роль в создании высококачественных изделий. Неправильный выбор режимов обработки или некачественная токарная обработка могут привести к снижению эксплуатационных характеристик изделий, увеличению производственных отходов и даже аварийным ситуациям. В этой статье мы подробно рассмотрим основные принципы токарной обработки стали, современные технологии и лучшие практики, чтобы помочь вам избежать ошибок и достичь оптимальных результатов.
Что такое токарная обработка стали?
Токарная обработка стали – это процесс механической обработки, при котором вращающаяся заготовка подвергается воздействию неподвижного режущего инструмента, называемого токарным резцом. При этом с заготовки снимается слой металла, что позволяет получить изделие с заданными размерами и формой. Этот метод широко используется для изготовления деталей, где требуется высокая точность и сложная геометрия: валы, оси, втулки, фланцы и многое другое. Токарную обработку можно проводить как на традиционных универсальных станках, так и на современных станках с ЧПУ, которые обеспечивают непревзойденную точность и повторяемость операций.
Ключевые функции и возможности токарной обработки стали
Современные технологии токарной обработки стали предоставляют огромный потенциал для создания изделий сложной геометрии, удовлетворяющих самым высоким требованиям к точности и качеству поверхности. Среди основных операций можно выделить:
- Наружное точение: Основная операция, позволяющая уменьшить диаметр заготовки или создать цилиндрические и конические поверхности. Например, при изготовлении вала двигателя наружное точение обеспечивает необходимую форму и равномерное распределение массы.
- Внутреннее точение (растачивание): Операция для обработки внутренних поверхностей, таких как отверстия в трубах или гильзах. Пример – увеличение диаметра внутреннего отверстия детали корпуса редуктора.
- Подрезка торцов: Создание плоских, перпендикулярных оси вращения поверхностей, что необходимо для изготовления фланцев, шайб и других крепежных элементов.
- Отрезка: Операция отделения части заготовки от основного материала, например, при производстве колец из стальной трубы.
- Нарезание резьбы: Процесс формирования наружной или внутренней резьбы, используемый для изготовления болтов, гаек и резьбовых соединений в трубопроводных системах.
- Проточка канавок: Создание углублений для размещения уплотнительных колец или стопорных элементов, что повышает функциональность деталей.
- Обработка фасонных поверхностей: Точная обработка сложных профилей и контуров с использованием специализированных резцов или ЧПУ станков, что особенно актуально при изготовлении пресс-форм и изделий сложной геометрии.
Современные токарные работы на ЧПУ позволяют автоматизировать процесс обработки, значительно повышая точность, производительность и повторяемость операций, что особенно важно для серийного производства.
Категории токарной обработки стали
Токарная обработка стали классифицируется по нескольким критериям, включая используемое оборудование, технологические методы и требуемую точность обработки. Основные категории включают:
- Черновая обработка: Осуществляется на начальном этапе для быстрого снятия большого объема материала. Здесь применяются более грубые режущие инструменты и допускаются большие отклонения, что позволяет быстро приблизить заготовку к требуемой форме.
- Чистовая обработка: Следующий этап, на котором заготовка обрабатывается с использованием более точных инструментов для достижения окончательных размеров и требуемой шероховатости поверхности.
- Прецизионная обработка: Выполняется с применением специальных станков и методов контроля для достижения максимально точных размеров и безупречного качества поверхности. Здесь используются современные технологии измерения и контроля.
- Обработка на универсальных станках: Традиционный метод с ручным управлением, требующий высокой квалификации оператора. Такие станки обладают большой гибкостью, но уступают по производительности и точности современным ЧПУ.
- Обработка на станках с ЧПУ: Высокотехнологичный метод, позволяющий автоматизировать процесс и обеспечить стабильное качество продукции. Особенно эффективен для серийного производства сложных деталей.
В зависимости от материала особенностями является, например, токарная обработка нержавейки, которая требует специализированных режимов резания и эффективного охлаждения.
Пошаговая инструкция по токарной обработке стали
Чтобы добиться наилучших результатов, важно четко следовать технологическому процессу. Представляем подробную пошаговую инструкцию:
- Подготовка:
- Анализ чертежа: Внимательно изучите чертеж, определив необходимые размеры, допуски и характеристики поверхности.
- Выбор заготовки: Подберите стальную заготовку с учетом припусков на последующую обработку.
- Подготовка станка: Проверьте техническое состояние станка, очистите его от стружки и убедитесь в корректной настройке.
- Выбор инструментов:
- Подбор резцов: Выберите резцы, изготовленные из быстрорежущей стали (HSS) или с твердосплавными пластинами, с учетом вида операции (черновая, чистовая, нарезание резьбы и т.д.).
- Проверка режущей кромки: Убедитесь в остроте и целостности режущей кромки, что напрямую влияет на качество обработки.
- Монтаж инструмента: Правильно установите резец в резцедержателе, соблюдая нужные углы и высоту для оптимальной обработки.
- Закрепление заготовки:
- Метод крепления: Выберите оптимальный способ закрепления (трикулачковый патрон, цанговый патрон или между центрами) в зависимости от формы заготовки.
- Надежность крепления: Убедитесь, что заготовка надежно зафиксирована, чтобы исключить биения и смещения во время обработки.
- Настройка режимов резания:
- Скорость резания: Определите оптимальную скорость резания, исходя из типа стали, материала резца и глубины резания. Неподходящая скорость может ускорить износ инструмента или снизить качество поверхности.
- Подача резца: Настройте подачу для достижения требуемой шероховатости и уменьшения вибраций. Оптимальные значения зависят от жесткости системы «станок-инструмент-деталь».
- Глубина резания: Установите соответствующую глубину резания, чтобы обеспечить нужный съём металла без перегрузки станка.
- Выполнение обработки:
- Запуск станка: Проверьте работоспособность всех систем и включите станок.
- Черновая обработка: Удалите основной объем материала, приближая заготовку к требуемым размерам.
- Чистовая обработка: Выполните финишную обработку для достижения окончательных размеров и качества поверхности.
- Охлаждение: Используйте подходящую охлаждающую жидкость для контроля температуры в зоне резания, что продлевает срок службы резца и улучшает качество обработки.
- Наблюдение за процессом: Постоянно контролируйте работу станка, следите за вибрациями и другими отклонениями, корректируя режимы при необходимости.
- Контроль качества:
- Измерения: После завершения обработки проверьте размеры детали с помощью штангенциркуля, микрометра или других измерительных приборов.
- Оценка поверхности: Проверьте шероховатость поверхности, используя профилометр или визуальный осмотр, чтобы удостовериться, что обработка соответствует заданным параметрам.
Совет: Регулярно затачивайте или заменяйте резцы и применяйте эффективные охлаждающие жидкости для улучшения качества обработки и продления срока службы инструмента.
Распространенные ошибки при токарной обработке стали и способы их предотвращения
Даже опытные специалисты могут допустить ошибки, которые негативно влияют на качество обработки и могут привести к серьезным последствиям. Рассмотрим основные ошибки:
- Неправильный выбор режимов резания: Использование неподходящих значений скорости, подачи или глубины резания может привести к быстрому износу инструмента, появлению вибраций и ухудшению качества поверхности.
- Последствия: Низкое качество обработки, ускоренный износ резца, повышенный риск поломки станка.
- Рекомендации: Экспериментируйте с режимами, начиная с рекомендованных значений для конкретного типа стали и инструмента, и постепенно оптимизируйте параметры.
- Недостаточная жесткость системы «станок-инструмент-деталь»: Неправильное крепление или слабые конструктивные элементы могут вызвать вибрации и биения.
- Последствия: Нарушение геометрии детали, ухудшение поверхности, аварийные ситуации.
- Рекомендации: Используйте более жесткие станки и приспособления, следите за состоянием оборудования и минимизируйте вылет инструмента.
- Игнорирование охлаждения: Недостаточное применение охлаждающей жидкости может привести к перегреву инструмента и заготовки.
- Последствия: Перегрев, ухудшение качества поверхности, быстрое разрушение резца.
- Рекомендации: Обеспечьте достаточное охлаждение, регулярно обновляйте жидкость и следите за её чистотой.
- Неправильная заточка резца: Тупой или неправильно заточенный резец увеличивает усилия резания, что приводит к вибрациям и ухудшению обработки.
- Последствия: Повышенные нагрузки на станок, ухудшение качества поверхности, быстрый износ инструмента.
- Рекомендации: Регулярно проверяйте и затачивайте резцы, соблюдая оптимальные углы заточки.
- Неправильное закрепление заготовки: Ненадежное крепление может привести к смещению заготовки и даже авариям.
- Последствия: Смещение заготовки, браковые детали, повышенный риск травматизма.
- Рекомендации: Используйте подходящие зажимы и регулярно проверяйте крепление детали перед началом обработки.
Соблюдение технологических режимов и правильная настройка станков, как описано в статье «Как избежать брака в производстве», помогут значительно повысить качество обработки и уменьшить риск ошибок.
Характеристики сталей для токарной обработки
Название стали | Свойства | Область применения | Особенности токарной обработки |
---|---|---|---|
Углеродистая сталь (например, Ст45) | Высокая прочность, хорошая обрабатываемость | Детали общего назначения, валы, оси | Легко обрабатывается, требует охлаждения при высоких скоростях |
Легированная сталь (например, 40Х) | Повышенная прочность, износостойкость, улучшенная закаливаемость | Шестерни, валы, детали, работающие при высоких нагрузках | Требует более твердого инструмента, умеренные скорости резания |
Нержавеющая сталь (например, 12Х18Н10Т) | Коррозионная стойкость, высокая прочность | Детали для агрессивных сред, медицинское оборудование, пищевая промышленность | Сложная обработка из-за высокой вязкости; требуется хорошее охлаждение и смазка, низкие скорости резания |
Инструментальная сталь (например, У8А) | Высокая твердость, износостойкость | Режущие инструменты, штампы, пресс-формы | Необходимы специализированные инструменты, низкие скорости резания, тщательный контроль температуры |
Автоматная сталь (например, А12) | Высокая обрабатываемость, низкая прочность | Мелкие детали для автоматизированного производства, крепеж | Легко обрабатывается на высоких скоростях, дает мелкую стружку |
Инновации и перспективы в токарной обработке стали
С развитием технологий токарная обработка становится все более автоматизированной и интегрированной с цифровыми технологиями. Станки с ЧПУ не только повышают качество изделий, но и оптимизируют процесс за счет автоматического контроля, анализа данных и предиктивного обслуживания оборудования. Новые материалы для режущих инструментов и передовые системы охлаждения позволяют существенно увеличить срок службы инструмента и улучшить качество обработки даже самых сложных сталей.
Также стоит отметить развитие интеграции с системами CAD/CAM, что позволяет создавать более сложные и точные изделия с минимальными затратами времени и ресурсов.
Токарная обработка стали от Симиди
Симиди – это производственно-инжиниринговая компания, специализирующаяся на изготовлении и поставке оборудования, узлов и деталей для промышленных предприятий. Мы предлагаем полный спектр услуг по токарной обработке стали с применением современных технологий и оборудования. Наши специалисты обладают высокой квалификацией и опытом, что позволяет гарантировать высокую точность и стабильное качество обработки.
Для получения дополнительной информации о наших услугах и возможностях вы можете уточнить детали или связаться с представителем компании.