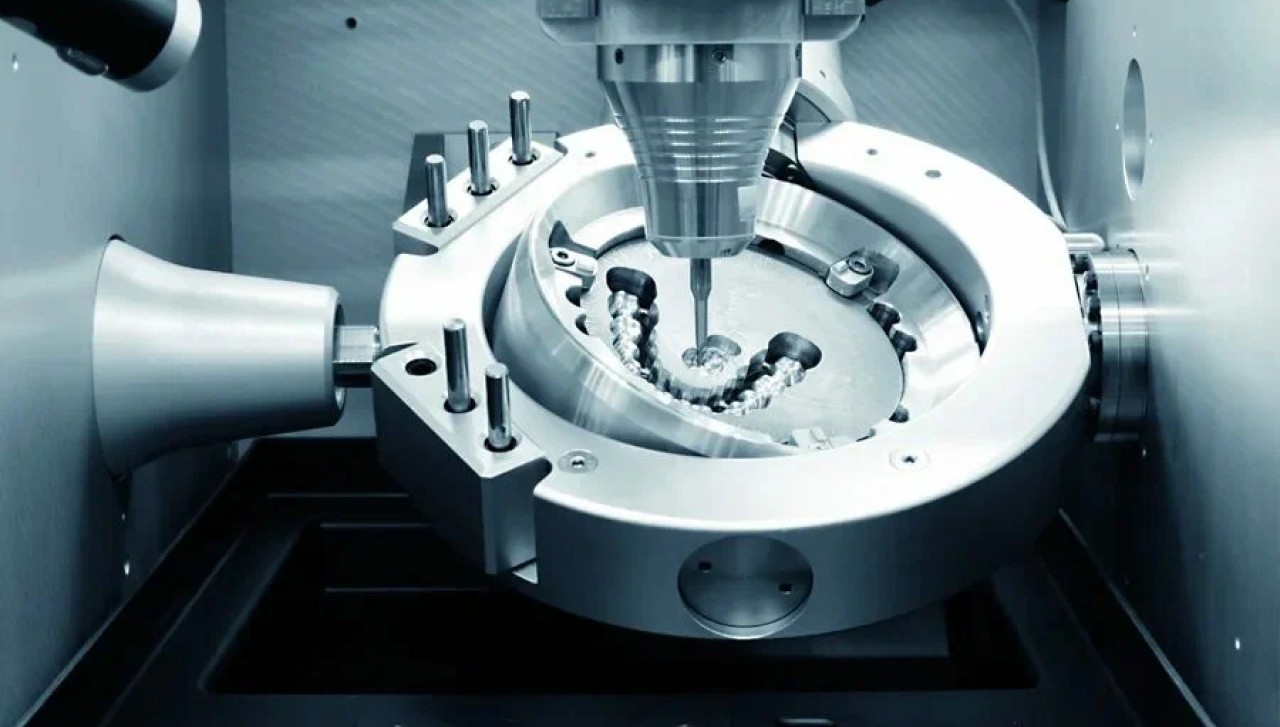
В современном производстве точность и быстрота играют ключевую роль. Представьте, насколько сложным был бы процесс изготовления даже самой простой детали без использования современных компьютерных технологий. Ошибка в расчетах, неоптимальный путь инструмента или неверный выбор режима резания могут привести не только к браку, но и к значительным потерям времени и увеличению себестоимости изделия.
В условиях высокой конкуренции и стремительного развития технологий игнорирование современных CAM-систем (Computer-Aided Manufacturing) становится серьезным препятствием для роста и эффективности производства. Отсутствие автоматизации, необходимость ручной настройки параметров обработки и сложность создания сложных траекторий движения инструмента создают массу проблем для предприятий, работающих по устаревшим технологиям.
Проблемы традиционных методов обработки
Специалисты, использующие традиционные методы программирования и ручную настройку станков, сталкиваются с рядом значимых трудностей:
- Высокая вероятность ошибок при ручном программировании, что часто приводит к браку готовых изделий.
- Длительное время подготовки управляющих программ, что снижает общую производительность.
- Ограниченные возможности обработки сложных геометрических форм, что требует дополнительных операций.
- Сложность оптимизации траектории движения инструмента, что повышает износ оборудования и инструмента.
- Проблемы при работе с различными типами станков и материалов, что ограничивает гибкость производства.
Что такое CAM-система?
CAM-система – это специализированное программное обеспечение, предназначенное для автоматизации подготовки производства. Она позволяет создавать управляющие программы для станков с числовым программным управлением (ЧПУ) на основе 3D-моделей деталей, связывая процессы проектирования (CAD) и непосредственного производства. Благодаря учету таких факторов, как геометрия детали, свойства материала, характеристики станка и режущего инструмента, CAM-системы позволяют формировать оптимальные стратегии обработки, минимизируя ошибки и повышая эффективность.
Ключевые функции и возможности современных CAM-систем
Современные CAM-системы обладают широким спектром функциональных возможностей, которые значительно упрощают и оптимизируют процессы фрезеровки и токарной обработки. Рассмотрим основные функции:
Автоматическая генерация траекторий инструмента. CAM-системы автоматически рассчитывают оптимальный путь инструмента на основе 3D-модели детали, что позволяет значительно сократить время подготовки управляющих программ и снизить вероятность ошибок. Например, при фрезеровке сложной поверхности система может учитывать кривизну и избегать потенциальных столкновений с заготовкой.
Моделирование процесса обработки. Многие современные решения предоставляют возможность визуальной симуляции процесса обработки. Такая функция позволяет заранее увидеть траекторию движения инструмента, оценить обрабатываемые области и выявить потенциальные проблемы – будь то столкновения с зажимами или некорректная траектория. Это особенно важно при работе с дорогими материалами и сложными конструкциями.
Оптимизация режимов резания. CAM-системы способны автоматически подбирать оптимальные режимы резания (скорость, подача, глубина резания) в зависимости от типа материала, характеристик инструмента и возможностей станка. Это не только повышает производительность, но и снижает износ инструмента, улучшая качество поверхности детали. Например, при обработке нержавеющей стали система может подобрать режимы, минимизирующие налипание материала на инструмент и предотвращающие его преждевременный износ. При необходимости выполнить Фрезеровку нержавейки, правильный подбор режимов резания становится критически важным.
Поддержка различных типов станков и инструментов. Современные CAM-системы адаптированы для работы с широким спектром оборудования – от токарных и фрезерных станков до токарно-фрезерных центров и электроэрозионных установок. Благодаря поддержке различных режущих инструментов, таких как фрезы, сверла и резцы, одна CAM-система может обслуживать множество производственных задач. Например, одна и та же система способна обеспечить программирование как простого токарного станка, так и сложного 5-координатного фрезерного центра.
Интеграция с CAD-системами. Интеграция с популярными CAD-системами позволяет напрямую импортировать 3D-модели без необходимости конвертации файлов. Это ускоряет подготовительный процесс и минимизирует вероятность ошибок. Так, при использовании модели, созданной в SolidWorks, интегрированная CAM-система может без проблем открыть файл детали и начать автоматизированное создание управляющей программы.
Классификация CAM-систем
Современные CAM-системы можно разделить на несколько категорий в зависимости от их функциональности и области применения:
2.5D CAM-системы. Эти системы предназначены для обработки деталей в двух с половиной координатах (X, Y, Z) и подходят для выполнения плоских операций, контурной обработки и сверления. Они широко применяются при изготовлении панелей, корпусов и других простых деталей.
3D CAM-системы. Предназначенные для работы в трех координатах, эти системы идеально подходят для обработки сложных геометрических форм, таких как пресс-формы, штампы и детали машин. Примером может служить изготовление скульптурных поверхностей или деталей с криволинейными элементами.
Многоосевые CAM-системы. Эти системы разрабатываются для станков с числом осей, превышающим три (например, 4- или 5-координатные станки). Они позволяют обрабатывать детали с нескольких сторон без необходимости переустановки заготовки. Например, 5 координатный станок позволяет создавать детали с поднутрениями и сложными криволинейными поверхностями, недоступными для станков с меньшим числом осей.
Специализированные CAM-системы. Существуют решения, ориентированные на конкретные задачи, например, для электроэрозионной обработки, зуборезных станков или станков для обработки листового металла. CAM-система для электроэрозионной обработки (EDM) позволяет создавать программы для вырезания сложных контуров и отверстий в деталях из твердых материалов.
Пошаговое руководство по созданию управляющей программы в CAM-системе
Ниже приведена подробная инструкция по созданию управляющей программы для фрезеровки детали:
- Импорт 3D-модели детали. На первом этапе модель, созданная в CAD-системе, импортируется в CAM-систему. Поддерживаемые форматы, такие как STEP, IGES или STL, обеспечивают гибкость работы с различными источниками данных.
- Выбор станка и инструмента. Определите станок, на котором будет выполняться обработка, и выберите режущий инструмент. Современные CAM-системы располагают обширными базами данных, позволяющими быстро подобрать оптимальные варианты для конкретных задач.
- Определение системы координат. Правильная настройка системы координат критична для корректной ориентации детали и точного позиционирования инструмента на станке.
- Выбор стратегии обработки. CAM-система предлагает различные стратегии – от черновой обработки до чистовой и карманной обработки. Выбор наиболее подходящей стратегии определяется характеристиками детали и требуемым качеством обработки.
- Настройка параметров обработки. Для каждой стратегии задаются параметры: скорость подачи, глубина и шаг резания, что позволяет адаптировать процесс под конкретные условия обработки.
- Генерация траектории инструмента. После настройки параметров система автоматически рассчитывает оптимальный путь инструмента, учитывая особенности 3D-модели и выбранную стратегию обработки.
- Моделирование процесса обработки. Перед запуском программы рекомендуется провести симуляцию, чтобы выявить возможные столкновения или ошибки в траектории движения.
- Создание управляющей программы. После успешного моделирования формируется управляющая программа в формате, поддерживаемом конкретным станком (например, G-код), что позволяет сразу приступить к обработке.
- Передача управляющей программы на станок. Финальным этапом является передача программы на станок с ЧПУ и запуск обработки, что запускает автоматизированный процесс изготовления детали.
Совет: Изучите документацию и пройдите обучение по работе с выбранной CAM-системой. Это поможет быстро освоить основные функции, избежать ошибок и значительно сократить время подготовки производства.
Распространенные ошибки при работе с CAM-системами и способы их предотвращения
Даже опытные специалисты могут столкнуться с ошибками в процессе работы с CAM-системами. Рассмотрим основные из них и способы их минимизации:
Неправильный выбор стратегии обработки. Неверно подобранная стратегия может снизить производительность и ухудшить качество обработки, а также привести к повреждению инструмента. Последствия: увеличение времени обработки, износ оборудования и появление брака. Рекомендации: детально анализируйте геометрию детали и выбирайте стратегию, соответствующую особенностям материала и требуемому качеству.
Некорректные параметры обработки. Установка слишком высоких скоростей подачи или чрезмерной глубины резания может привести к поломке инструмента и повреждению детали. Последствия: аварийные остановки, дорогостоящий ремонт и потери в производстве. Рекомендации: руководствуйтесь рекомендованными параметрами и учитывайте характеристики используемого станка и инструмента.
Игнорирование моделирования процесса обработки. Пренебрежение предварительным моделированием может обернуться столкновениями инструмента с заготовкой или вспомогательными элементами оборудования. Последствия: повреждение станка, инструментов и деталей, а также риск получения травм персоналом. Рекомендации: всегда проводите симуляцию перед запуском программы, чтобы гарантировать безопасность и точность обработки.
Неправильная настройка системы координат. Ошибки при установке координат приводят к смещению детали, что негативно сказывается на качестве готового изделия. Последствия: брак, необходимость переделки и потеря времени. Рекомендации: тщательно проверяйте настройки системы координат перед началом обработки, чтобы избежать неточностей.
Отсутствие учета особенностей станка. Некоторые CAM-системы могут не учитывать индивидуальные характеристики конкретного оборудования, что приводит к неоптимальной траектории движения инструмента. Последствия: снижение производительности, ухудшение качества поверхности и риск повреждения оборудования. Рекомендации: выбирайте CAM-системы, адаптированные под ваш тип станка, либо вносите необходимые корректировки в настройки обработки.
Сравнение характеристик CAM-систем
Ниже представлена сравнительная таблица, демонстрирующая ключевые особенности различных CAM-систем:
Название | Свойства | Область применения | Особенности |
---|---|---|---|
Система A | Широкий набор функций, интеграция с CAD, поддержка многоосевой обработки | Авиационная промышленность, автомобилестроение, машиностроение | Высокая стоимость, требует квалифицированного персонала |
Система B | Простой интерфейс, доступная цена, подходит для 2.5D и 3D обработки | Небольшие мастерские, учебные заведения | Ограниченная функциональность, нет поддержки многоосевой обработки |
Система C | Специализированная система для электроэрозионной обработки, автоматическая оптимизация траектории | Производство пресс-форм, штампов, сложных деталей из твердых материалов | Узкая специализация, высокая стоимость |
Выбор CAM-системы и преимущества сотрудничества с Симиди
Выбор подходящей CAM-системы является ключевым шагом на пути к повышению эффективности и качества производства. При выборе учитывайте свои производственные задачи, бюджет, а также уровень квалификации персонала. Инвестиции в современную CAM-систему – это инвестиции в будущее вашего предприятия, позволяющие не только оптимизировать процессы, но и повысить конкурентоспособность на рынке.
Компания Симиди – это надежный партнер в области производственно-инжиниринговых решений. Мы не только поставляем современное оборудование и компоненты, но и оказываем всестороннюю поддержку нашим клиентам. Благодаря глубокому пониманию производственных процессов и богатому опыту, мы помогаем предприятиям внедрять передовые технологии автоматизации.
Свяжитесь с нами, чтобы получить консультацию по выбору оптимального решения для вашего производства и узнать о наших возможностях в области Токарно-фрезерные работы на ЧПУ. Мы готовы предложить индивидуальный подход и помочь вам добиться максимальной эффективности и качества обработки.