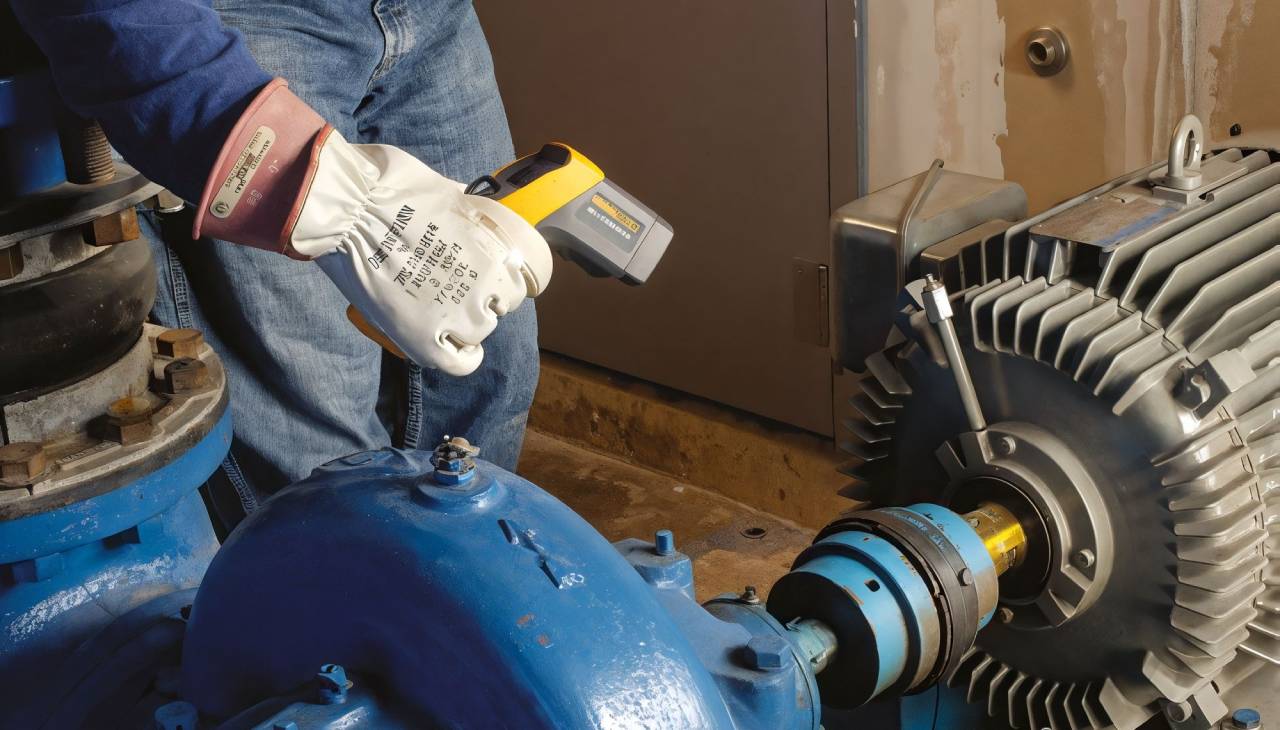
Современная металлообработка требует высокой точности и надёжности, особенно когда речь идёт о создании сложных деталей и узлов. Для достижения высоких стандартов качества необходимо использовать передовые технологии измерений, которые позволяют контролировать параметры готовой продукции с минимальной погрешностью.
Одной из таких технологий являются бесконтактные методы измерения, которые активно применяются в металлообработке и помогают обеспечить высокий уровень контроля качества. В этой статье мы рассмотрим, что представляют собой бесконтактные методы измерения, их преимущества и применение в промышленности.
Что такое бесконтактные методы измерения?
Бесконтактные методы измерения — это технологии, которые позволяют проводить измерения размеров, формы и других характеристик объекта без прямого физического контакта с ним. Такие методы используются для измерения как готовых деталей, так и промежуточных заготовок, чтобы убедиться в их соответствии заданным стандартам и спецификациям. В отличие от традиционных контактных методов измерения, бесконтактные технологии не воздействуют на измеряемый объект, что позволяет избегать механических повреждений и неточностей, вызванных деформацией поверхности.
Советы по использованию бесконтактных методов измерения:
- Выбирайте подходящий метод для конкретной задачи: лазерная триангуляция хорошо подходит для сложных форм, а ультразвуковые датчики — для измерения толщины.
- Учитывайте тип материала: для прозрачных или полупрозрачных материалов оптические датчики могут быть более эффективными.
- Обеспечьте правильную калибровку: регулярная калибровка оборудования важна для достижения максимальной точности измерений.
Основные бесконтактные методы измерения
Существует несколько ключевых бесконтактных методов измерения, которые нашли широкое применение в металлообработке. Рассмотрим некоторые из них:
Лазерная триангуляция
Лазерная триангуляция является одним из самых распространённых методов бесконтактного измерения. Она основана на использовании лазерного луча, который направляется на поверхность детали, а затем отражается и фиксируется приёмным устройством. Расстояние между лазерным датчиком и поверхностью определяется на основе геометрии треугольника, что позволяет получить точные данные о форме и размерах детали. Лазерная триангуляция широко используется для измерения сложных поверхностей, где требуется высокая точность и быстрота измерения.
Совет: Используйте лазерную триангуляцию для объектов со сложной геометрией, где важна высокая скорость измерений.
Оптические датчики и системы сканирования
Оптические системы позволяют получать данные о размерах и форме деталей с помощью световых лучей и камер. Они могут включать в себя 2D- и 3D-сканеры, которые создают детализированную модель объекта, фиксируя каждую деталь с высокой точностью. Оптические системы особенно полезны для измерения поверхностей с большим количеством деталей и сложных геометрических форм, таких как криволинейные поверхности. Эти системы активно применяются в автомобильной и авиационной промышленности, где важна высокая точность изготовления деталей.
Совет: Оптические датчики идеально подходят для деталей, требующих сканирования со всех сторон, чтобы создать трёхмерную модель.
Видеометры
Видеометры используют камеры для захвата изображения детали и программное обеспечение для анализа полученных данных. Видеометры позволяют измерять размеры и контролировать геометрию деталей без необходимости контакта с объектом. Этот метод подходит для контроля малых деталей и компонентов, а также используется для измерений в условиях, когда контакт с поверхностью нежелателен из-за риска её повреждения.
Совет: Применяйте видеометры для мелких деталей, где важно быстрое и точное измерение без физического воздействия.
Ультразвуковые датчики
Ультразвуковые датчики применяются для измерения толщины и структуры металлических заготовок. Они работают по принципу отражения ультразвуковых волн от поверхности объекта и определения времени их возврата. Этот метод позволяет измерять толщину стенок труб, резервуаров и других объектов, где важно поддерживать определённые размеры без повреждений. Ультразвуковые датчики также могут использоваться для обнаружения внутренних дефектов, таких как трещины или пустоты.
Совет: Используйте ультразвуковые датчики для контроля толщины и выявления внутренних дефектов, особенно в труднодоступных местах.
Вихретоковые датчики
Вихретоковые датчики используются для контроля поверхности металла и выявления дефектов, таких как трещины, коррозия и другие неоднородности. Они работают на основе индукции вихревых токов в материале и анализа изменений магнитного поля. Этот метод позволяет выявлять дефекты даже на глубине нескольких миллиметров под поверхностью, что делает его особенно полезным для контроля качества в авиакосмической и энергетической промышленности.
Совет: Вихретоковые датчики хорошо подходят для контроля поверхностей на наличие дефектов, включая трещины и коррозию.
Преимущества бесконтактных методов измерения
Использование бесконтактных методов измерения в металлообработке имеет ряд важных преимуществ, таких как:
- Высокая точность: Бесконтактные методы позволяют проводить измерения с высокой точностью, что особенно важно при производстве сложных деталей с минимальными допусками. Отсутствие механического воздействия на деталь снижает вероятность искажения результата.
- Быстрота измерений: Бесконтактные методы обеспечивают быструю проверку параметров детали, что ускоряет производственный процесс и позволяет проводить контроль качества в реальном времени. Это особенно важно в условиях серийного производства, где каждая минута играет роль.
- Измерение сложных форм: Традиционные методы измерения могут быть неэффективны при работе с деталями сложной геометрии. Бесконтактные методы позволяют измерять криволинейные и сложные формы с высокой точностью, что делает их незаменимыми для таких отраслей, как авиастроение и автомобилестроение.
- Отсутствие повреждений: При контактных методах измерения может возникать риск повреждения поверхности изделия, особенно если речь идёт о мягких материалах. Бесконтактные методы позволяют избежать таких повреждений, что особенно важно при работе с изделиями высокого качества.
- Интеграция в производственный процесс: Современные бесконтактные системы могут быть легко интегрированы в производственные линии, что позволяет автоматизировать контроль качества и повысить его эффективность. Интеграция систем числового программного управления (ЧПУ) с бесконтактными измерениями позволяет достигать высокого уровня автоматизации.
Применение бесконтактных методов измерения в металлообработке
Бесконтактные методы измерения нашли широкое применение в различных отраслях металлообработки:
- Автомобилестроение: Использование оптических и лазерных систем позволяет измерять геометрию кузовных деталей, обеспечивая высокую точность и надёжность производства.
- Авиакосмическая промышленность: В авиастроении важно обеспечить абсолютную точность всех деталей, так как малейшие отклонения могут привести к серьёзным последствиям. Оптические сканеры и вихретоковые датчики используются для контроля качества компонентов.
- Производство труб и резервуаров: Ультразвуковые датчики позволяют измерять толщину стенок и выявлять дефекты на этапе производства, что важно для обеспечения безопасности эксплуатации продукции.
- Судостроение: В судостроительной промышленности бесконтактные методы помогают контролировать качество металлических листов и конструкций, что повышает надёжность и долговечность готовых изделий.
Симиди: высокоточные изделия и надёжное качество
Наши специалисты используют лазерные, оптические и ультразвуковые технологии для контроля качества на каждом этапе производства. Обращайтесь в компанию Симиди, чтобы заказать серийное изготовление, фрезеровку стали или токарные работы на ЧПУ, выполненные с применением современных методов контроля. Мы гарантируем высокую точность и надёжность нашей продукции, что является залогом вашего успеха.